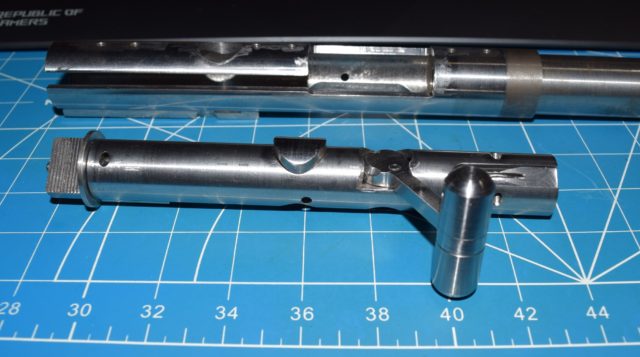
Talk to any mechanical engineer that is into guns and you will probably find out that they want to design the perfect straight pull bolt action rifle. I have no idea why this is but it seems to be as common as OCD is with engineers and I’m no exception.
I started out in the petrochemical field with my first engineering job. Eventually I got restless doing mechanical engineering on petrochemical things and started to dream up designs of guns in my spare time. I was lucky at the time and was able to get some of the CAD designers at my job to teach me enough about AutoCAD to start learning it on my own.
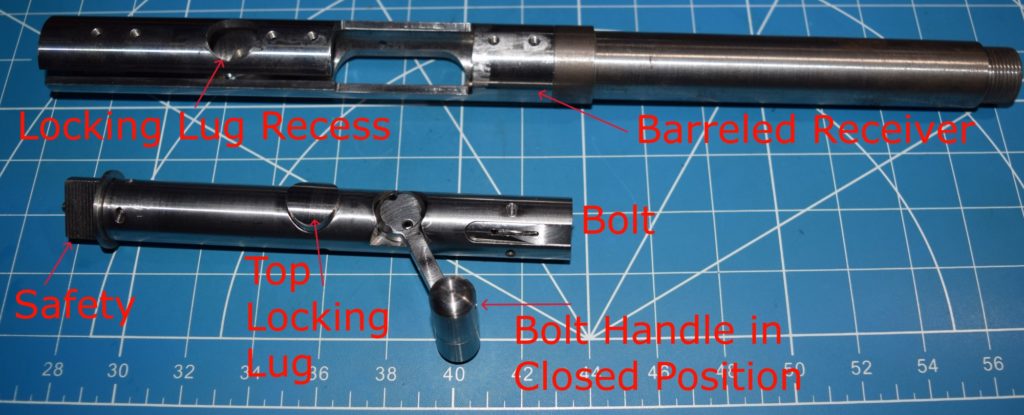
I was also lucky in that I met Robert Pauza about this same time working at my local gun shop. Those not familiar with Robert’s work might know him for his P-50, 50 caliber gas operated semi automatic rifle used in the movie RoboCop2 (“Cobra Assault Cannon”). Robert and I were talking one day when the subject of the AWC Centurion integrally suppressed 45 ACP bolt action rifle came up. The military Special Forces had purchased some of these weapons from AWC to use for clandestine removal of sentries and guard dogs. The action, a standard two lug turn bolt action, was designed and manufactured by Robert Pauza. He turned around and plucked his prototype from his pile of guns and told me to take it to the range to test it out. The rifle was not suppressed but it was the same action and stock with a 16 in (406mm) barrel. He did not have to ask me twice, so off to the range I went. What he had done was equivalent to giving drugs to a drug addict and I was hooked. There is something about firing those subsonic 45 caliber slugs at 100 yrds without any appreciable recoil. He of course was not selling his prototype (I keep my prototypes as well) and AWC had long ago sold out of the guns to the military. I was not deterred, I had to design one for myself but it had to be, you guessed it, a straight pull action!
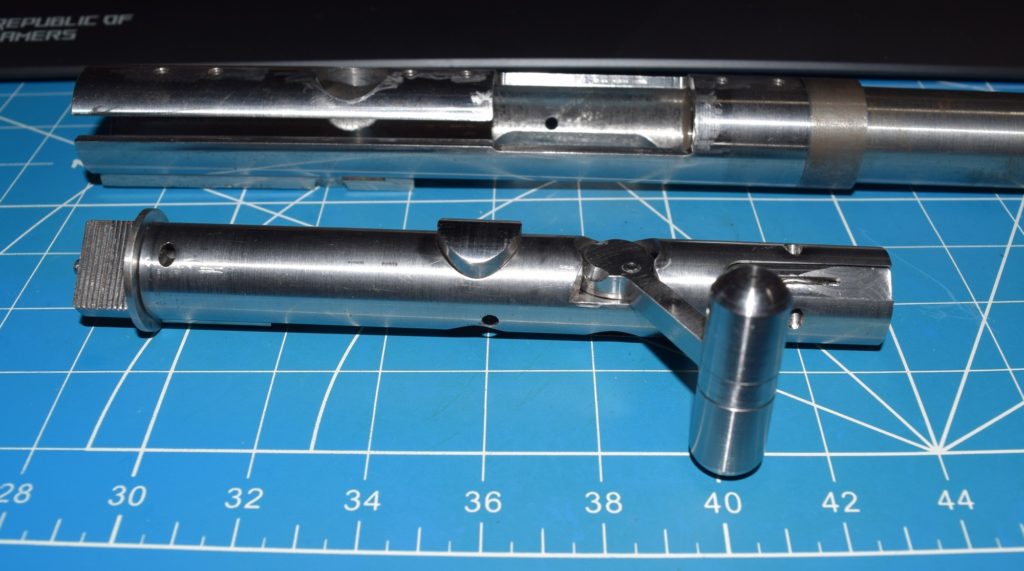
I had the skills (I’m an ME, we know everything), I had the tools (aka AutoCAD self semi- taught) and I had the OCD to do this! The next 6 months I spent my lunch hours and after hours working on my new super weapon. I was constantly designing and redesigning, making it more perfect in each time. I added neat features like a tritium dot that would glow red to the shooter when the safety was off and green when it was on. I slimmed down the action to save weight and even added CO2 purging for the suppressor using air gun cartridges so there would be no first round pop. I generated a set of drawings for the parts and a sectioned view drawing to show how it worked and everything looked great. Unfortunately, I did not have any experience at the time applying tolerances to my design since my engineering experience up to this point dealt with +/- 1/8 inch (3.2mm) on items like pressure vessels and towers that were hundreds of feet high. A secret that is not told outside of engineering circles most of the time is that colleges do not teach engineers how to do their jobs. The college only teaches the engineer how to approach a problem and the mathematical tools to analyze problems but everything else you need in your engineering job will be taught to you when you get to your job by the senior engineers in the company. I am an excellent mechanical engineer in the petrochemical field but only slightly above a numb nut in the firearms design at the time. Machinists refer to engineers with this level of experience as a dumb ass.
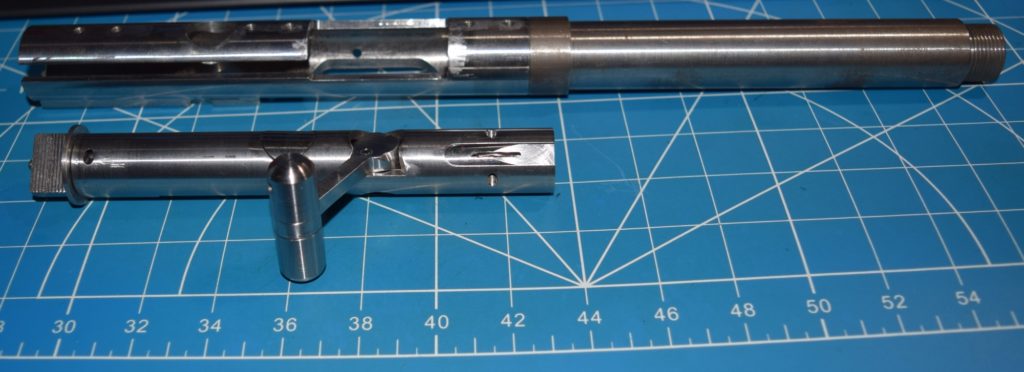
Some time passed until I was working with a machine shop on another project and we get around to talking about guns after a meeting one day (a seemingly common occurrence in Texas). I mention my design and that it’s ready to go with drawings and everything. The owner gets intrigued and offers to machine the prototype for me. I hand over my set of drawings and explain how it’s suppose to work and he oohs and awes and then says to give him a few weeks. I am sure there are still machinist in his shop that retired years later complaining about that damn gun drawn up by that damn dumb ass.

Months later, the owner and I met and he hands me a bag of the most beautifully machined parts that I had seen. There were even two sets of parts in the bag so I can put together two prototypes! The owner then says he thinks there might be an issue with my design since he can’t figure out how to get it together. I point out that in the sectioned view where all the parts go and how they work; it is just a matter of putting it together.
I hurried home with my bag of soon to be guns and spread them out on my work bench with my gunsmith tools. I start assembling my master piece and the first part fits fairly tight but that can be fixed later on some design tweaking. The third part did not fit at all. Looking at I realize that the first part kept the third part from fitting into it. The eye brows were getting closer together quickly as my brow was wrinkling up in thought as to how I could design something that obviously fit together when assembled but could not be assembled. Hours later and a few extra holes being drilled into a few of the new parts to try to get clearance to assemble some of the pins I finally succumb to the realization that my first gun design is an utter flop.
I still have that bag of parts 25 years later and I keep it as my bag of shame to remind me that even an engineer can be a dumb ass. Unfortunately I have long ago lost the AutoCAD files of the drawings and these days I use SolidWorks as my design tools. SolidWorks is a 3D computer design tool that gives the user the ability to operate the design and even assemble it to hopefully catch errors like mine before it ever gets to the machinist.
I present to you, my shame aka my design. In reviewing my bag of parts for this article my dream of designing a straight pull bolt action 45 ACP rifle has been sparked again, we will see.
Design criteria:
- Cock on opening, one of the hardest design goals to do in a bolt action straight pull.
- Feed from a 1911 magazine.
- Safety features to include method for handling high pressure gas in the event of a case head or primer failure.
- Primary extraction not a high priority due to 45 ACP or 9mm Luger chambering.
- Inert gas purging of the suppressor to eliminate first round pop. Use of “air gun” CO2 cartridge or N2 cartridge for the purging.
- Tritium vials in the safety to show its status in the dark.
- Light weight as possible. Reduce action diameter to a minimum to achieve size reduction and weight.
Mongo
www.John1911.com
“Shooting Guns & Having Fun”
- What is it – Weird Optics From The Past - April 18, 2024
- Design Disaster – A Lesson in Firearms Engineering - November 2, 2023
- Mongo’s Spare Parts Rifle No. 2 - October 1, 2023